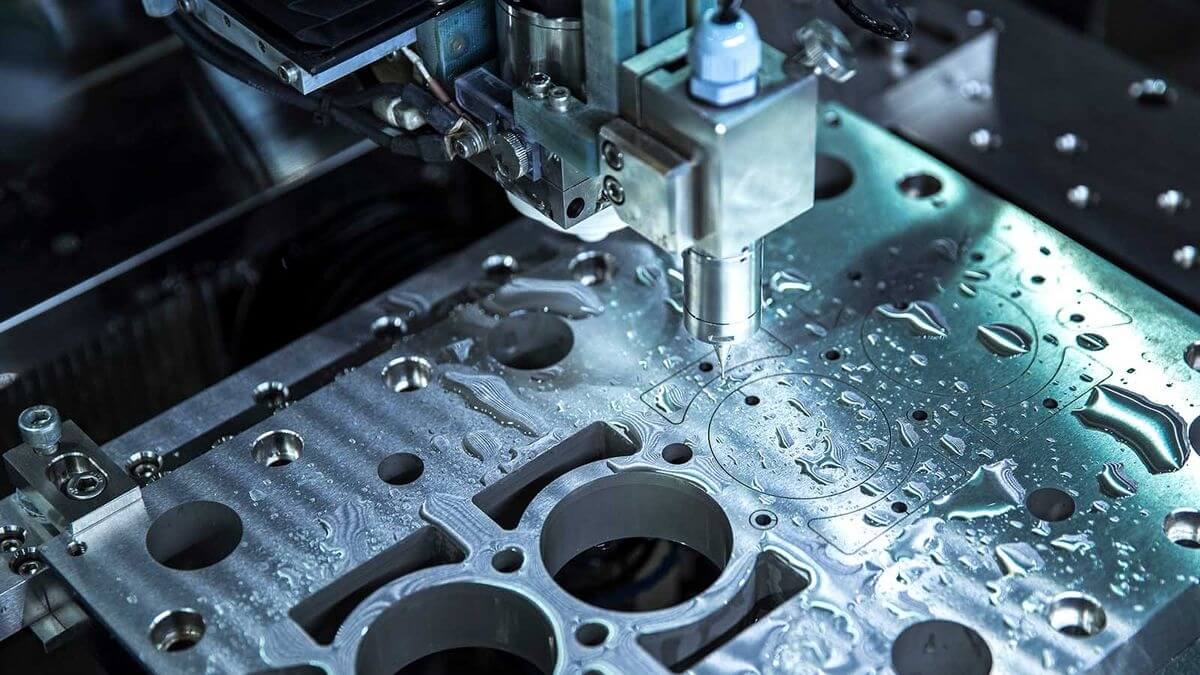
Online CNC machining service
On-demand CNC machining service for rapid prototyping and production parts, through a network of specialized, experienced and thoroughly vetted local and global CNC machine shops.
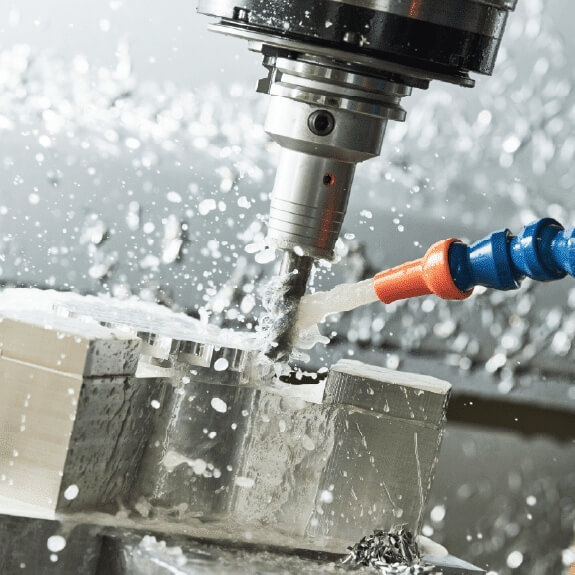
Precision CNC Machined Parts
Achieve consistent, high-quality parts for prototyping and manufacturing precision with CNC machining
From quick metal components to complex, mission-critical parts, Nexus Technologies Incorporation offers the right tool for the job at hand.
CNC machining allows for hitting tight tolerances and high repeatability with every order.
If you’re in need of production-grade metal materials, prototypes or production runs and quick turnaround times, our machining team can help.
How CNC Machining Works
Rather than building parts layer by layer like additive technology, CNC machining starts with a solid stock piece and cuts away material – leaving behind a finished part.
Starting with an STP file and 2D drawing, our team programs and validates the operations that the mill follows.
Once finished parts are created, secondary options like smoothing, polishing, painting and more can be performed.
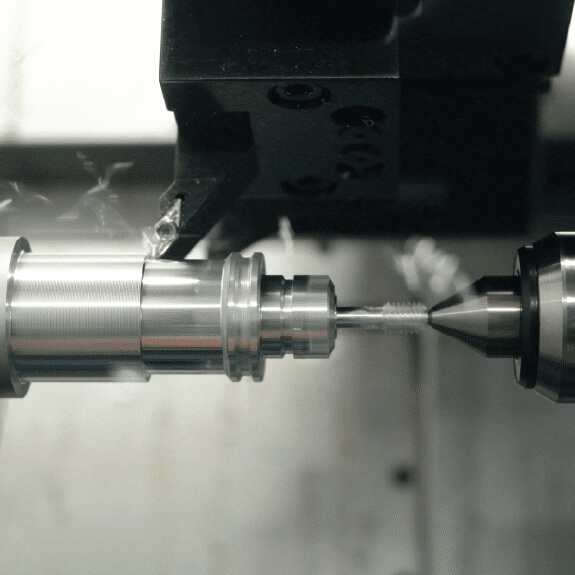
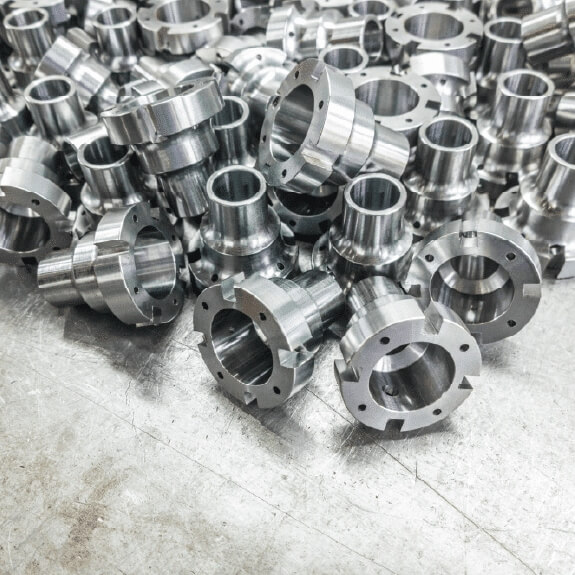
Common Applications
Explore popular uses for this traditional manufacturing method
- Medical
- Automotive
- Military
- Aerospace
- Consumer goods
Gallery of CNC machined parts
Here’s a small selection of the CNC machined prototypes and end-use parts we’ve produced for our customers.
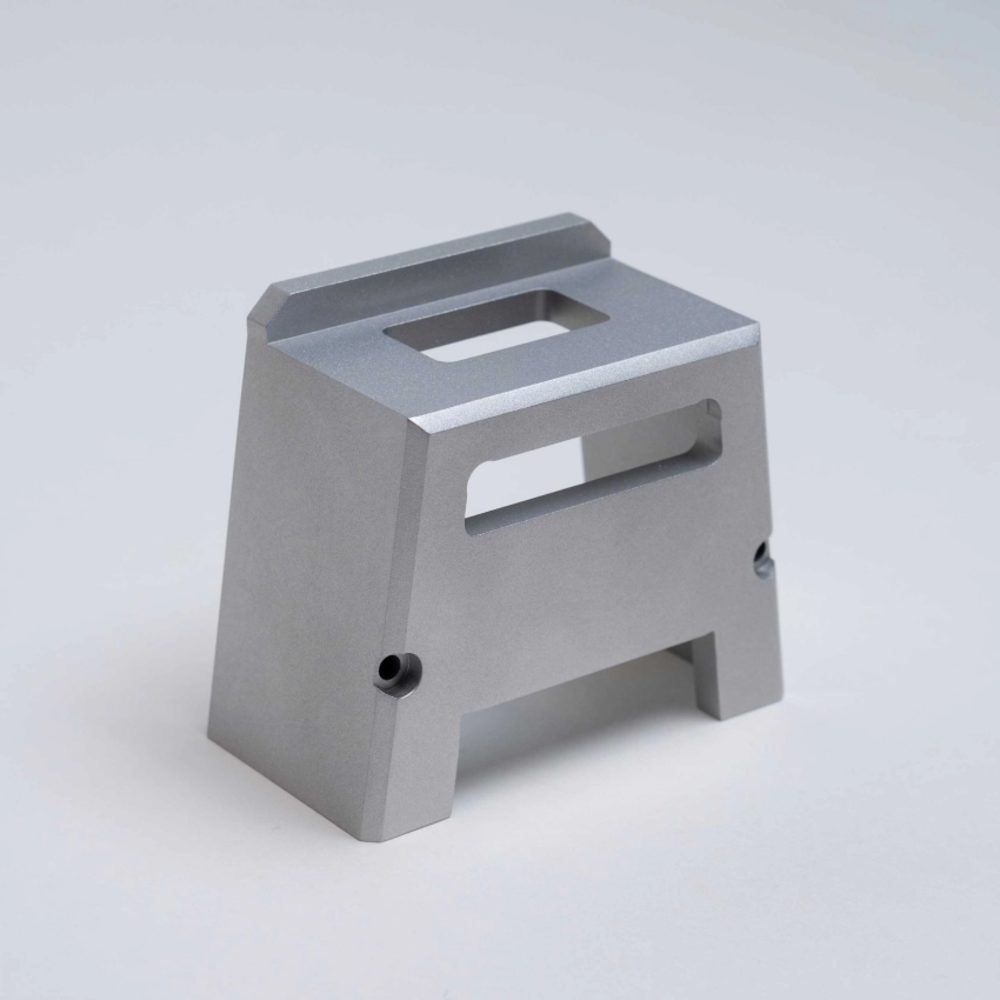
Aluminium 7075-T6
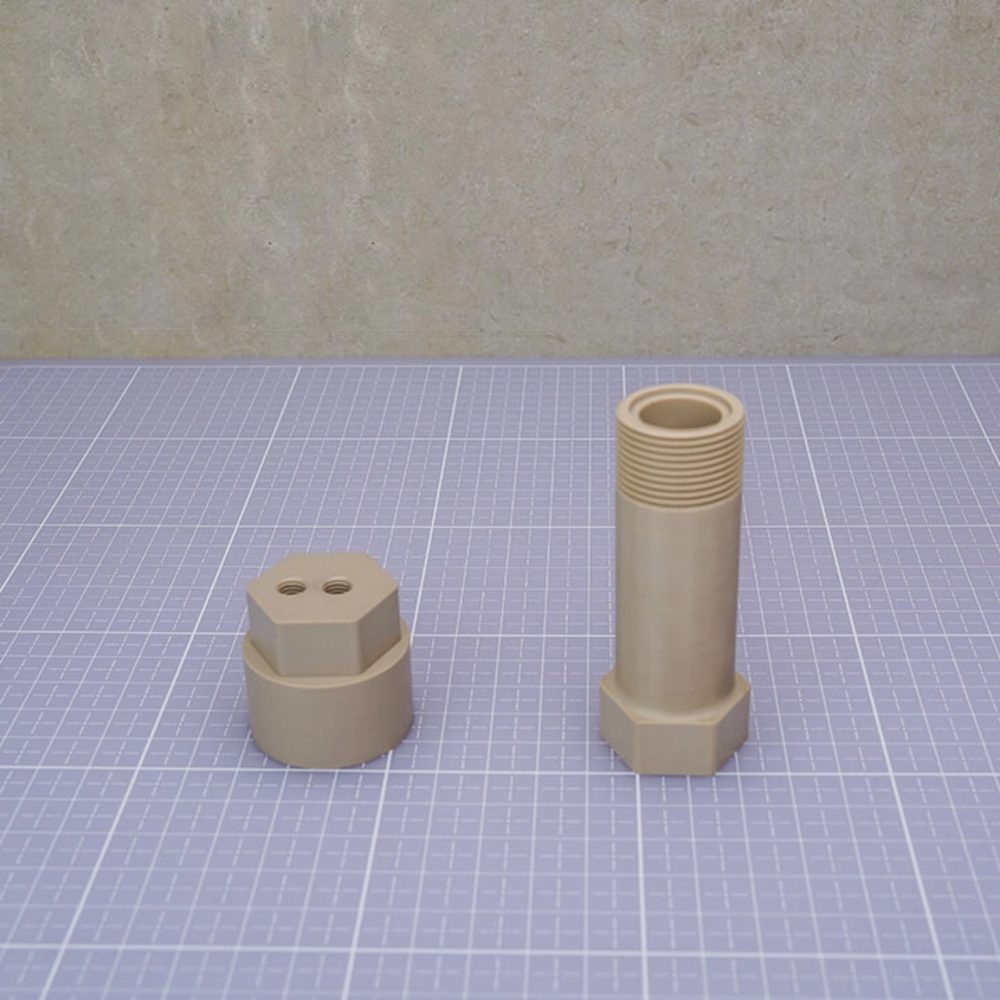
PEEK
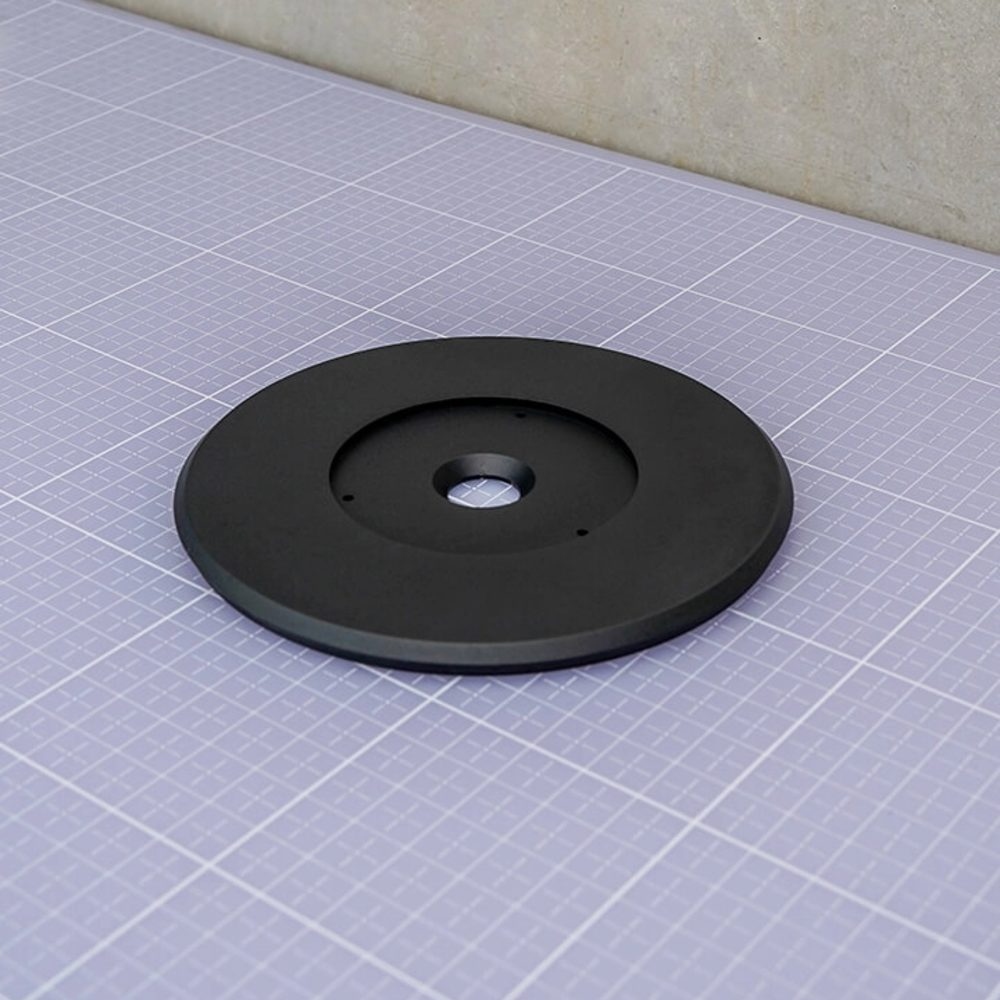
Alumium 6063
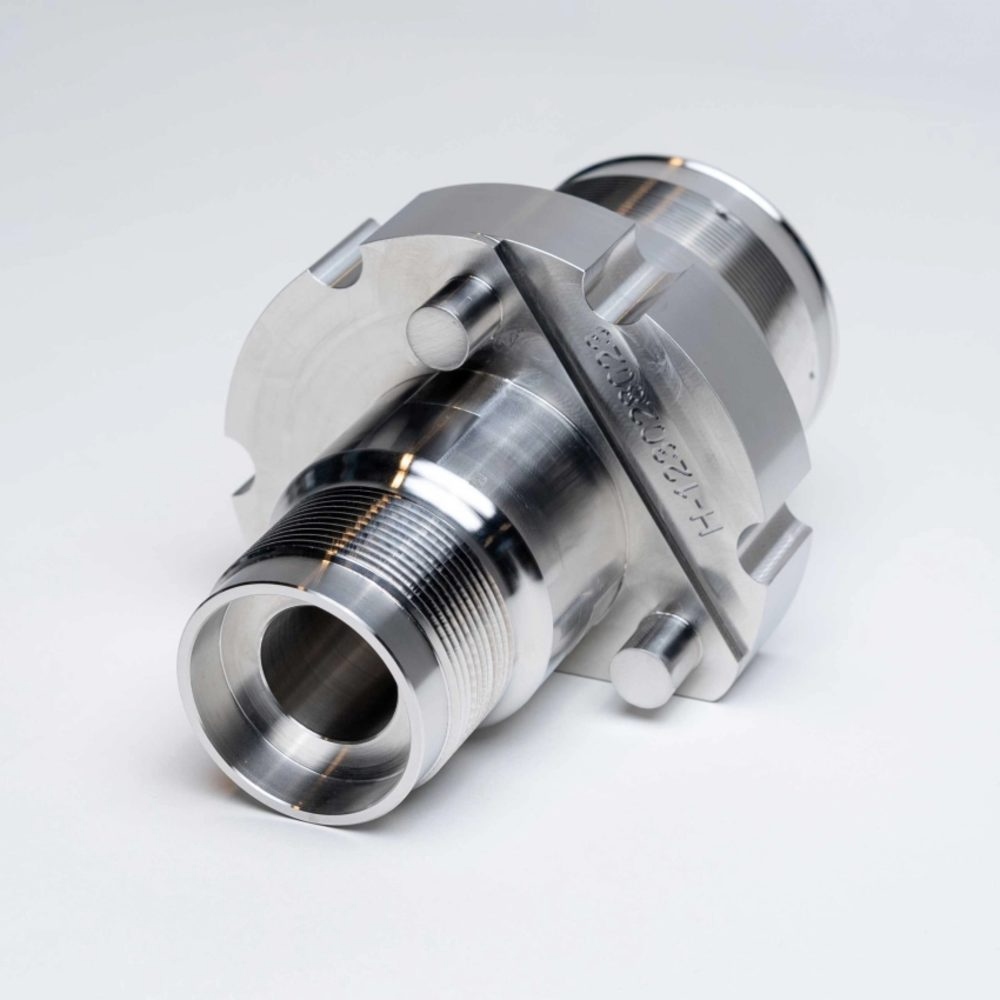
Stainless steel 304
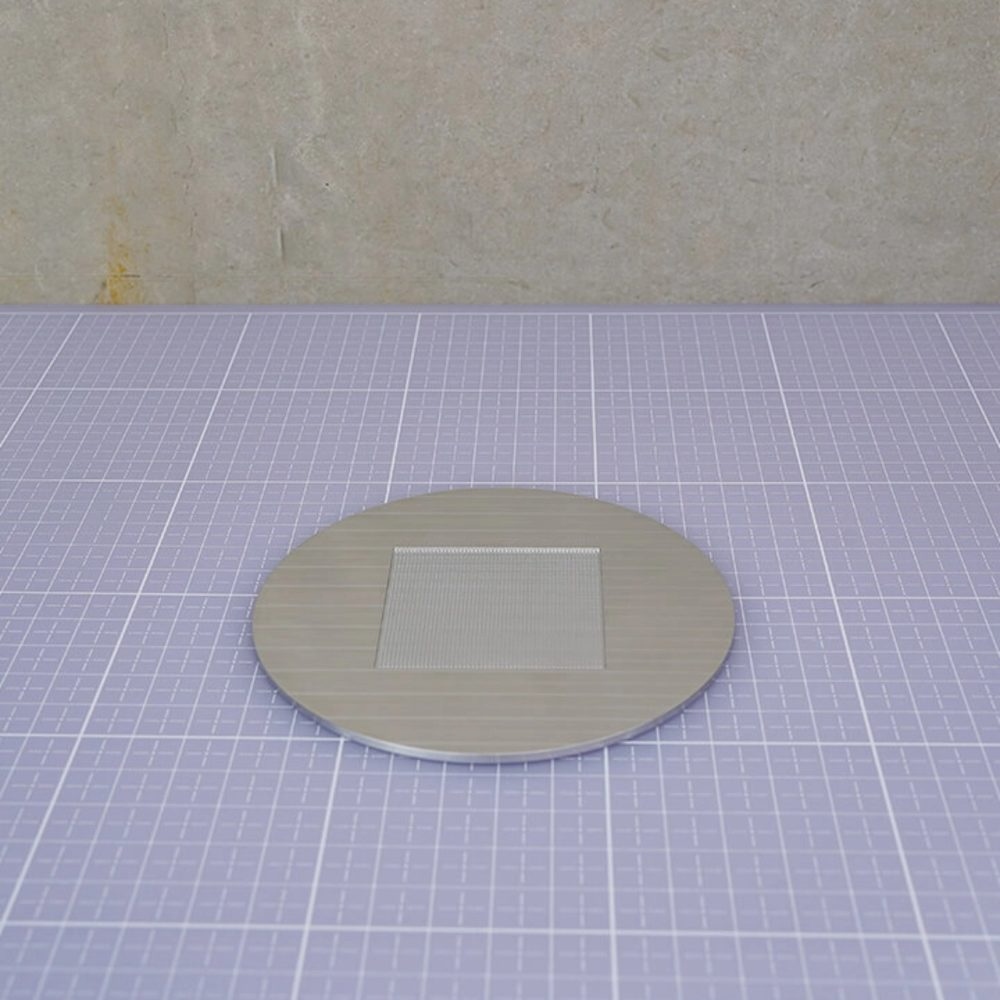
Aluminum 6082
CNC machining surface finishes
We can instantly quote a wide variety of post-machining surface finishes.
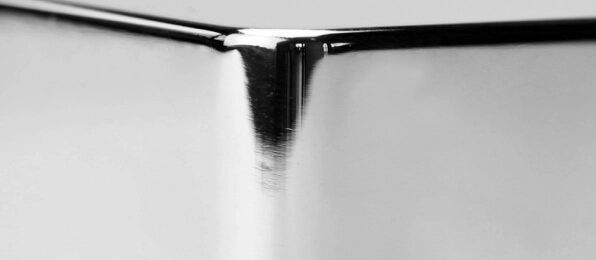
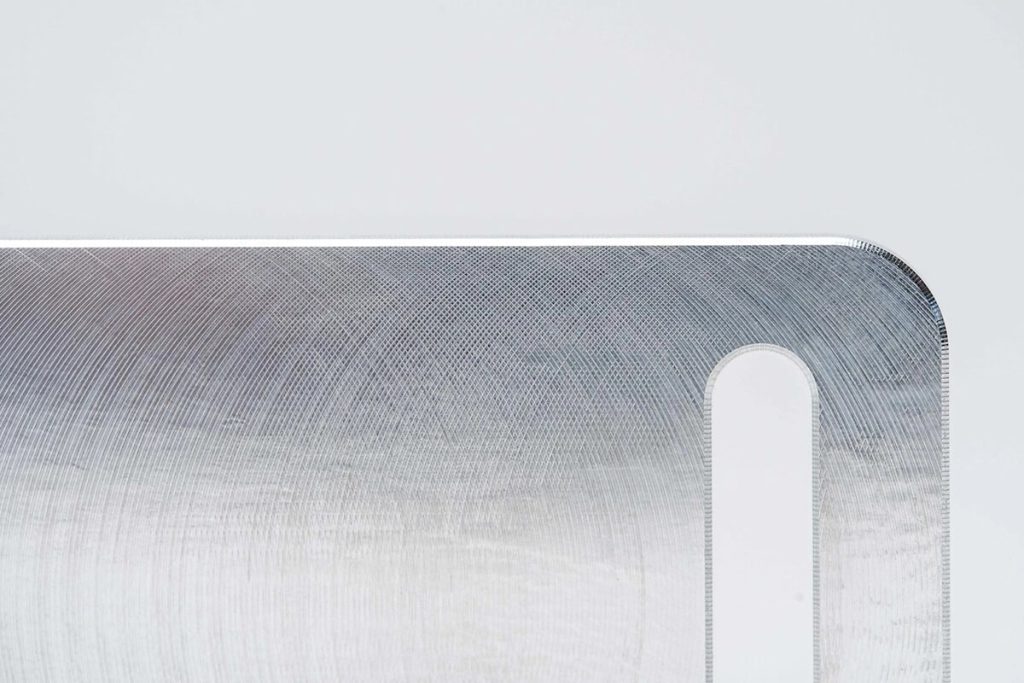

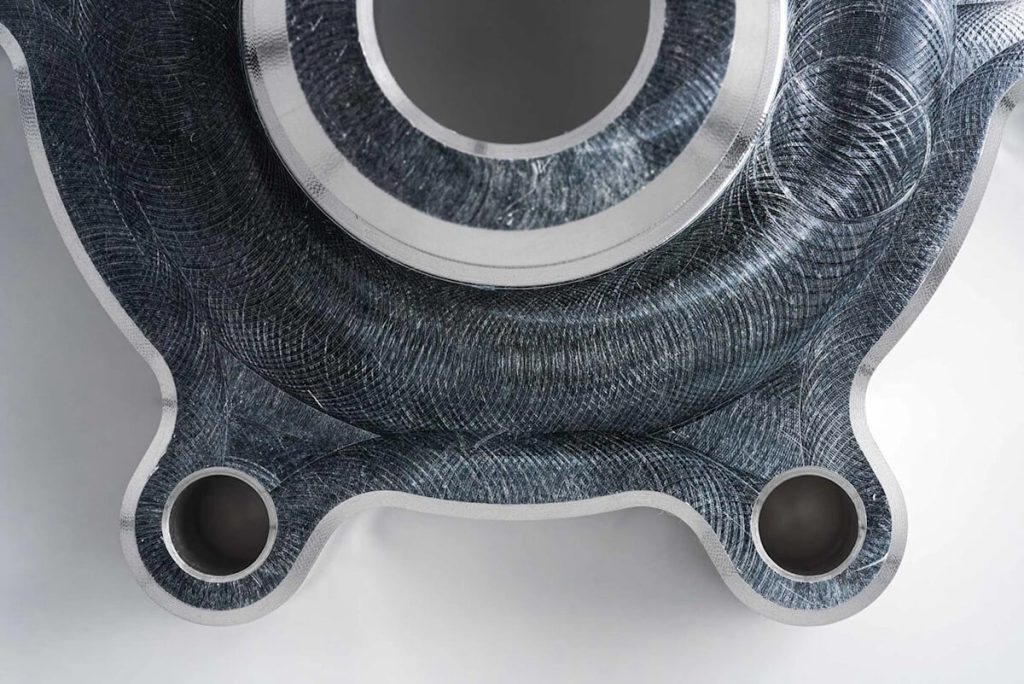
Technical Specifications
Tolerance Accuracy Range | Default: +/- 0.005" ∘ Small features and holes: +/- 0.001-0.002" ∘ Features over ~10" pick up ~0.001 in/in |
Metal Materials | Aluminum 6061, Brass, Copper, Cold Rolled Steel, Mild Steel, Stainless Steel |
Plastic Materials | ABS, Acrylic, Delrin, HDPE, Nylon, PEEK, Polycarbonate, Polypropylene, Ultem, Teflon |
Frequently Asked Questions
The location and accessibility of a part’s features will dictate how many set-ups or operations are required. Parts with multiple set-ups may suffer a small tolerance loss between features. Multiple operations can also affect a project’s cost and lead time.
Reach VS WidthLong, thin cutters deflect and break. When reaching into a deep pocket, keep radii large to accommodate a thicker, more robust cutter. Internal Stresses Residual internal stresses in the workpiece, coupled with elevated temperatures involved in the cutting operation, can cause parts to deflect. This effect is exacerbated when a large amount of material is being removed from a thin, flat workpiece.
Radii and Tool AccessRotating cutting tools are essentially cylinders, meaning that internal vertical corners need a radius, if only a small one. If the cutting tool is unable to reach a feature, it cannot be CNC machined. Careful tool selection can reach some mild undercuts, but, as a general rule, all features should be line-of-sight. This effect is exacerbated when a large amount of material is being removed from a thin, flat workpiece.
Due to this process, some visible tool marks may be seen.
If additional finishing is required, please note in your drawings and in your request for a quote.
Anodized, bead blast, chem film, passivation, and powder coat.